Custom Electronics Design for a Vital Health and Safety Wearable
In 2016, Reactec approached us to tackle mechanical challenges for their first wearable design. Impressed with our initial work, they returned for the complete package of hardware and industrial design of their next-generation device. With a tight development schedule for a custom electronics design and the need for state-of-the-art (unreleased) hardware components, it was a tough challenge within a complex supply chain environment.
Here’s how we focused on the electronics and software aspects to achieve a fantastic design for Reactec.
Client
Reactec
Work category
Services
Prototyping & Testing
Electronic Engineering
Software Development
Mechanical Engineering
Industrial Design
Manufacturing Support
Project Management
Multiple communication protocols.
NFC, BLE, and UWB.
Project Brief
Reactec tasked us with designing the hardware and mechanical enclosure for the second-generation of their HAVs (Hand-arm vibration) monitoring device. The R-Link watch not only measures and warns users about unsafe vibration levels from machinery but also integrates Ultra Wide Band (UWB) technology for proximity detection within the R-Link system.
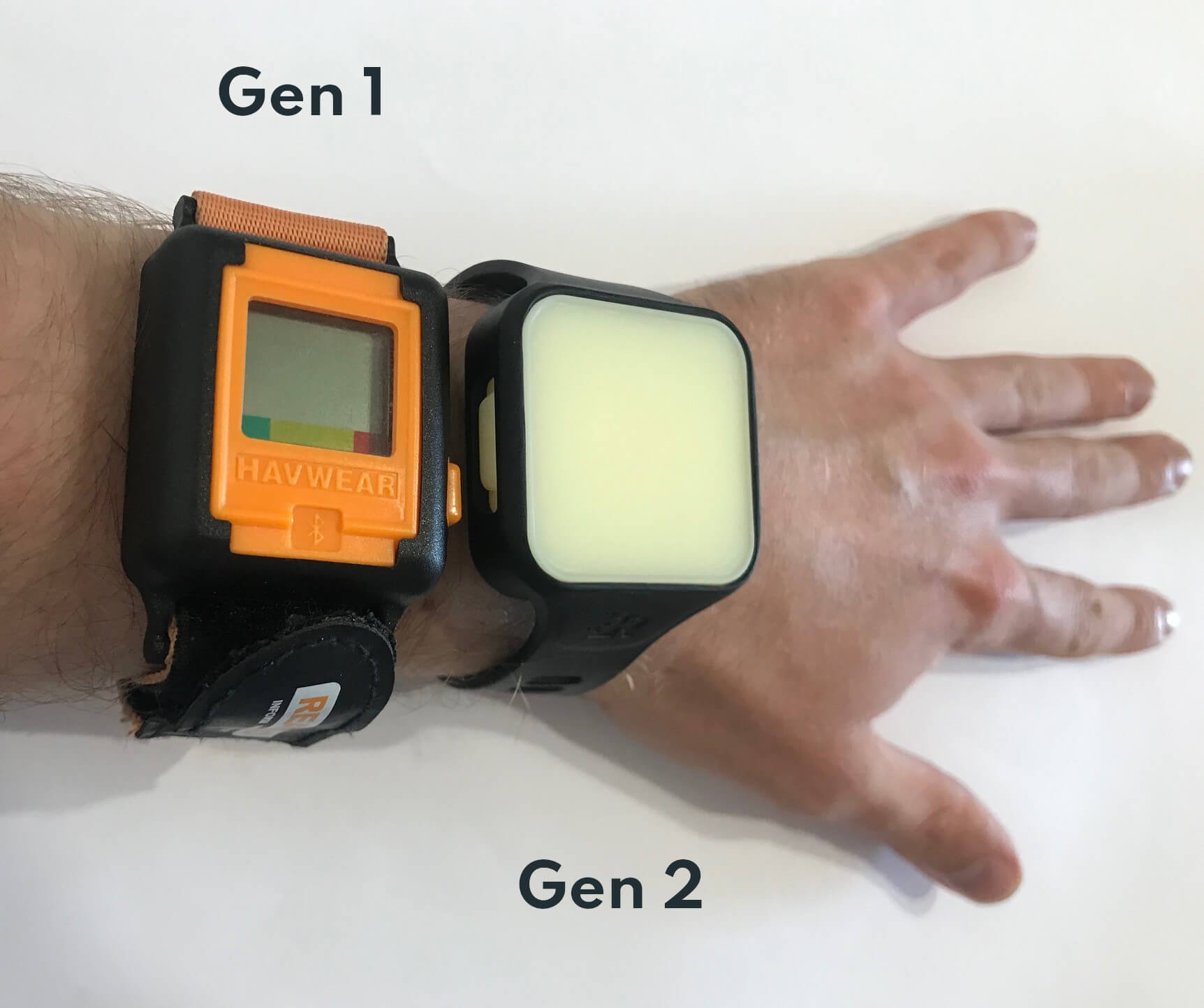
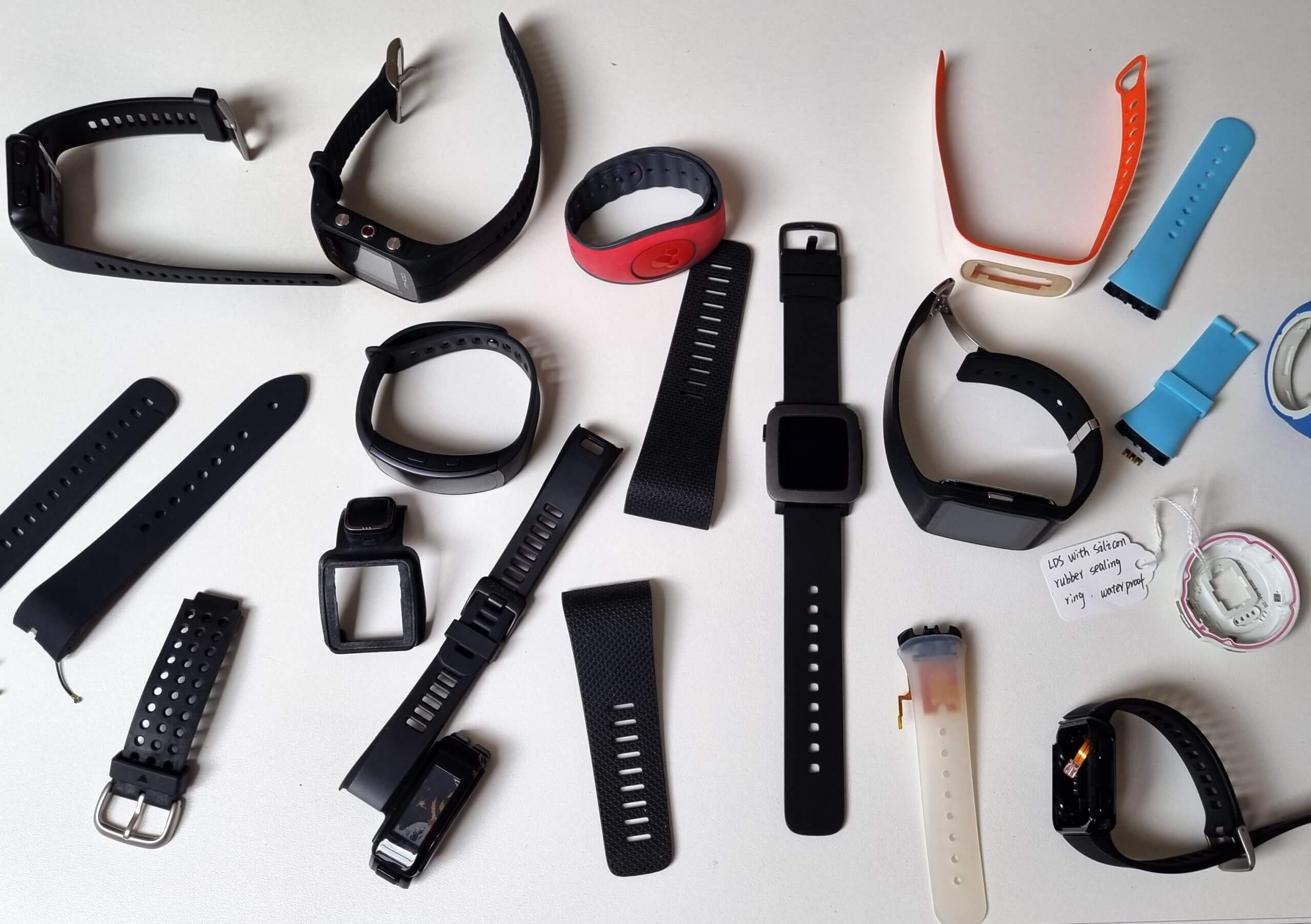
Our goal was to use our knowledge in product design and custom electronics design to balance the device’s functionality, aesthetics, manufacturability, and usability, including a detachable “smart” module for hygiene and multi-user flexibility.
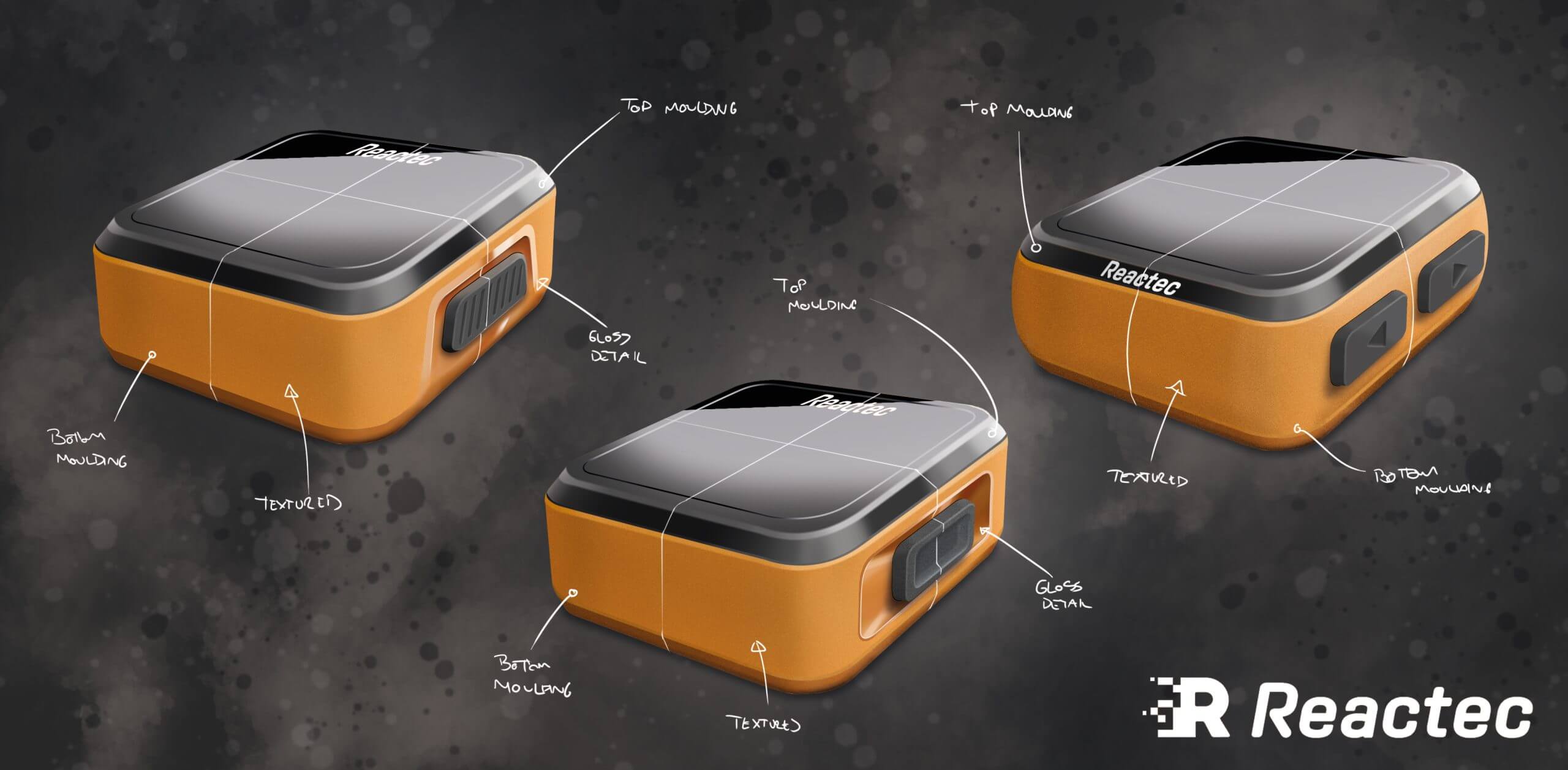
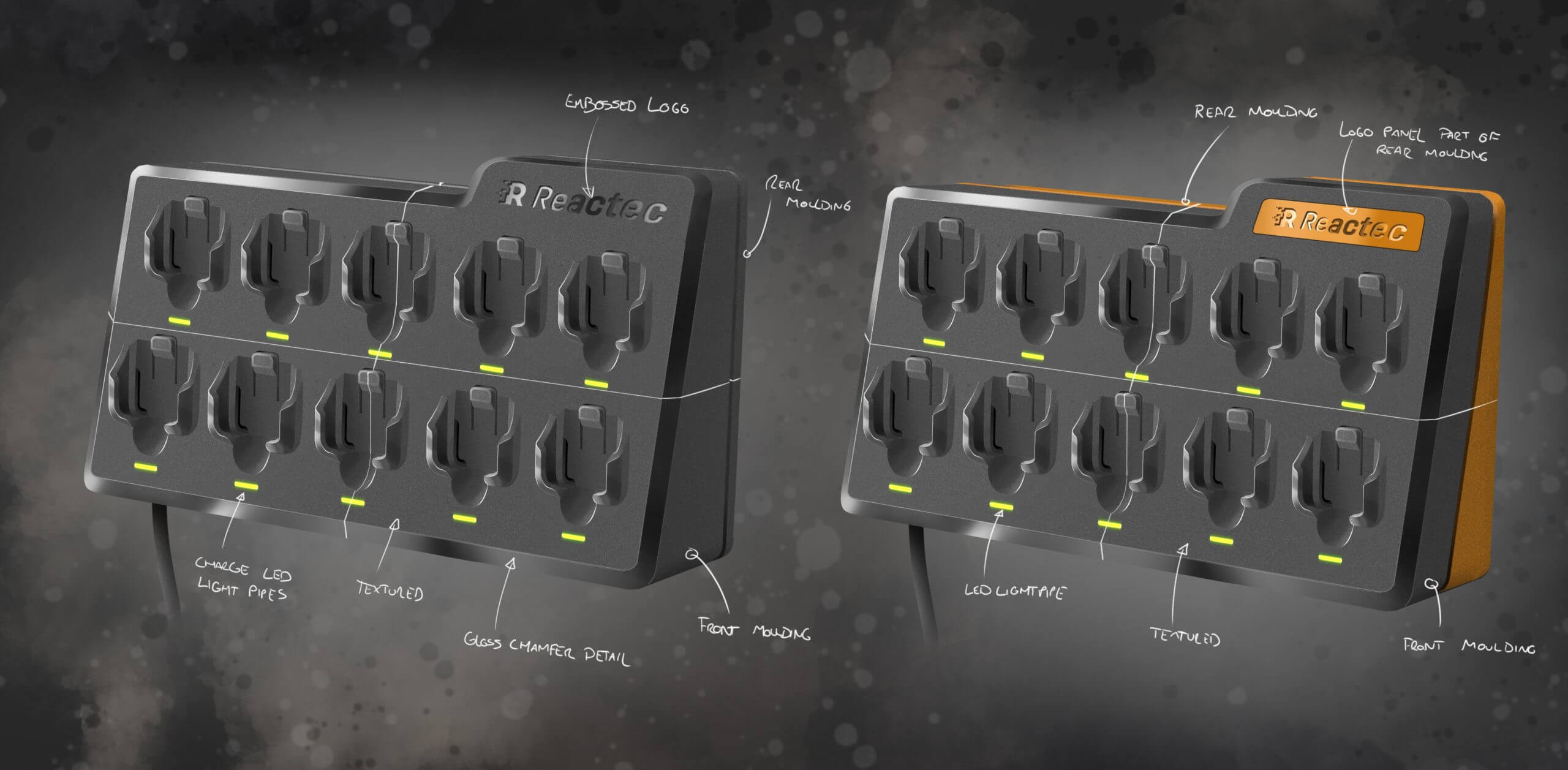
“The electronic & mechanical design of the product has been very efficiently executed.”
— Leif Anderson, CTO of Reactec Ltd.
Approach
Our extensive experience in electronics for wearables informed our two-stage approach to mitigate hardware design risks early:
- Initial Development Stage:
We designed and prototyped an oversized PCB featuring all the products functionalities with numerous test points and modular connections. This served as a development tool for Reactec’s firmware engineers, enabling early work and providing a platform for testing and verifying high-risk design components. - Final Miniaturisation Stage:
After validating the initial design, we shrunk the PCB to fit the wearable’s form factor, incorporating any changes identified during the first stage. Although debugging at this size is challenging, prior validation made the testing process run smoothy.
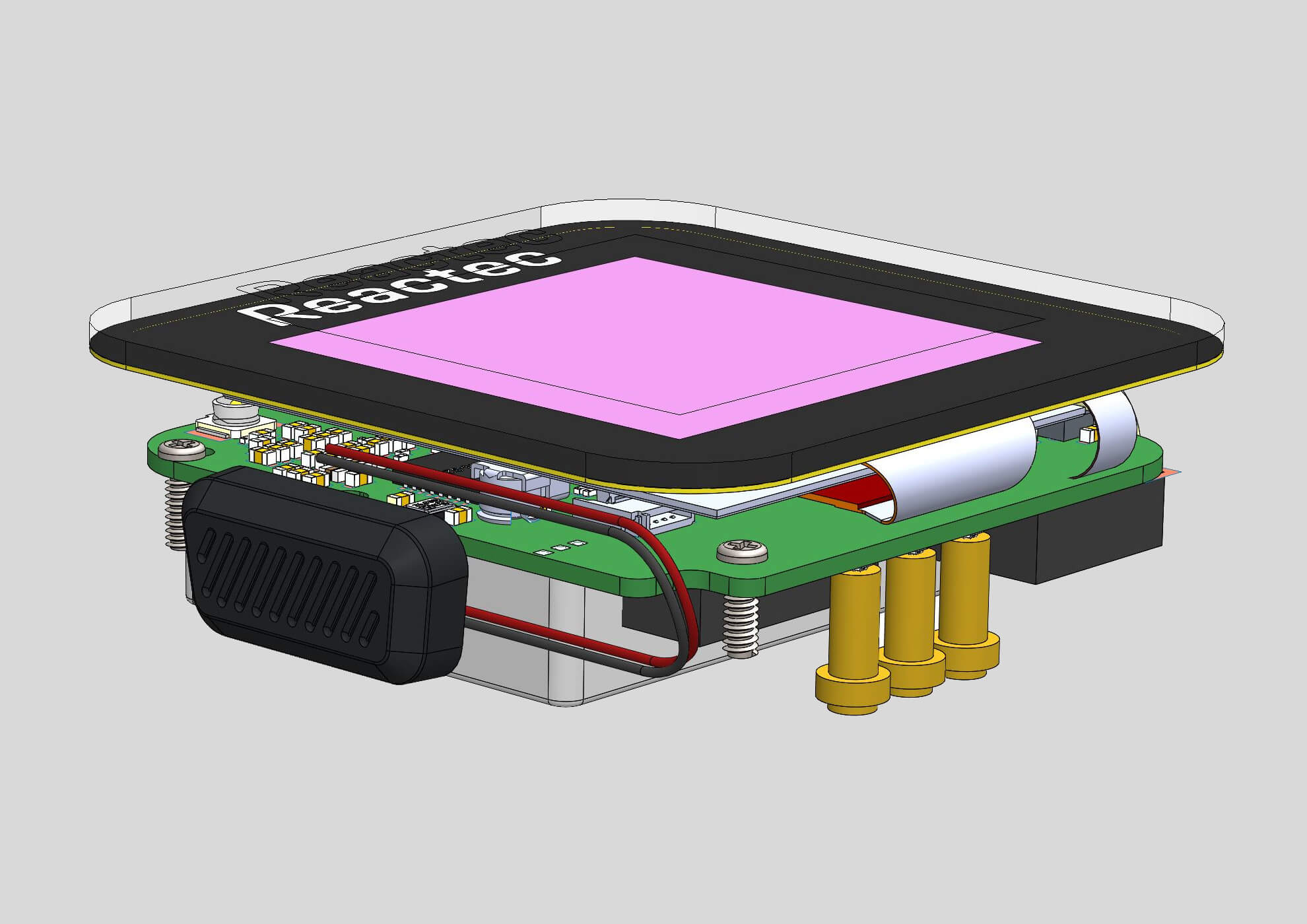
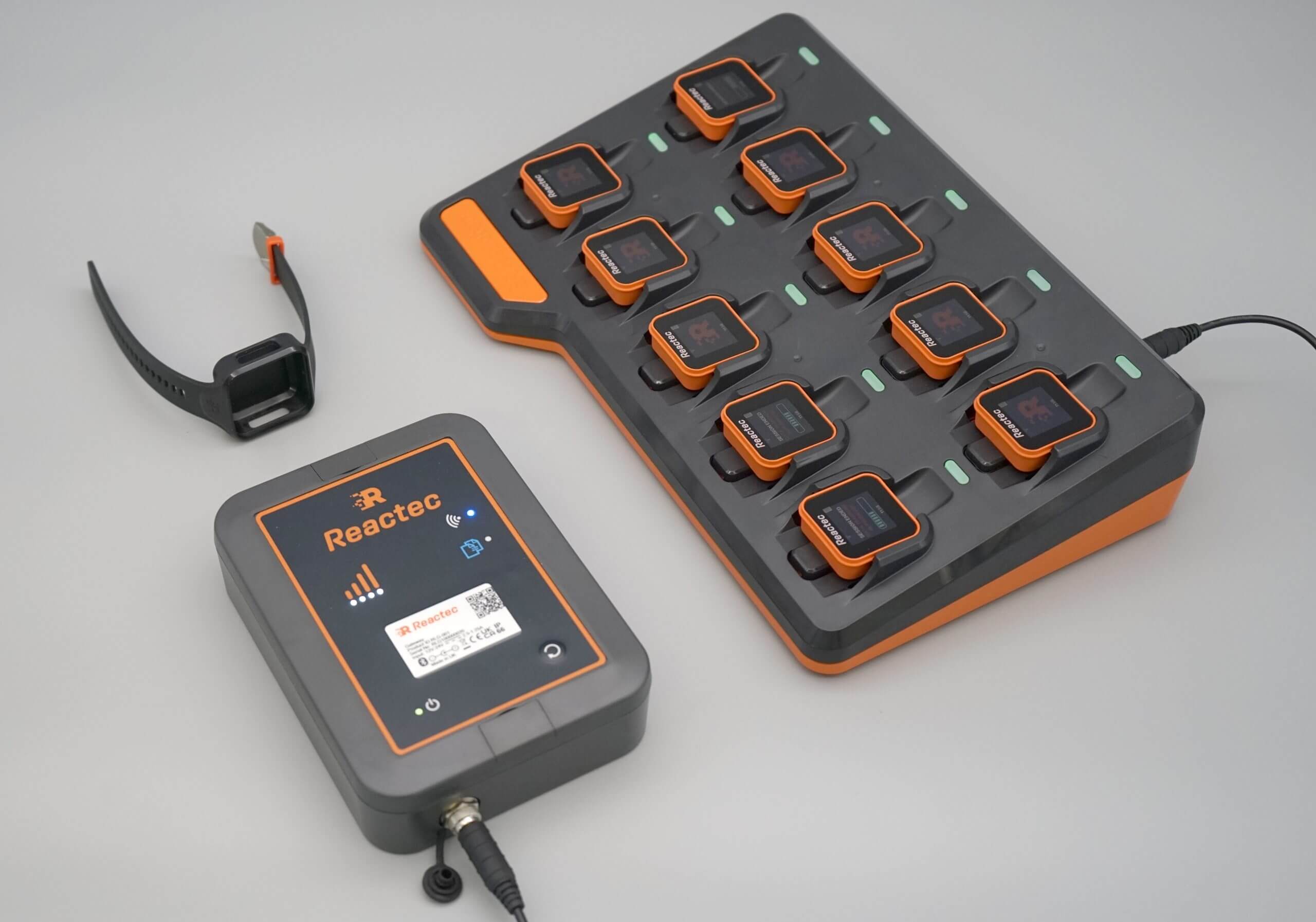
Reactec’s internal team provided detailed design specifications and participated in regular reviews, supporting our team in testing the wearable and its charging dock. Concurrently, they developed the embedded software for the wearable and electronics for the R-Link beacons.
Result
The final product blends consumer-grade aesthetics with industrial-grade functionality. The wearable and docking station showcase the high-density PCB assembly and compact integration of battery, antennas, and display, achieved through close collaboration between our electronic and industrial design teams.
This product helped Reactec cement their vision of transforming industrial workplace health risk management from reactive to proactive. The R-Link system addresses various exposure risks, including Hand Arm Vibration, dust, noise, proximity, and lone working conditions.
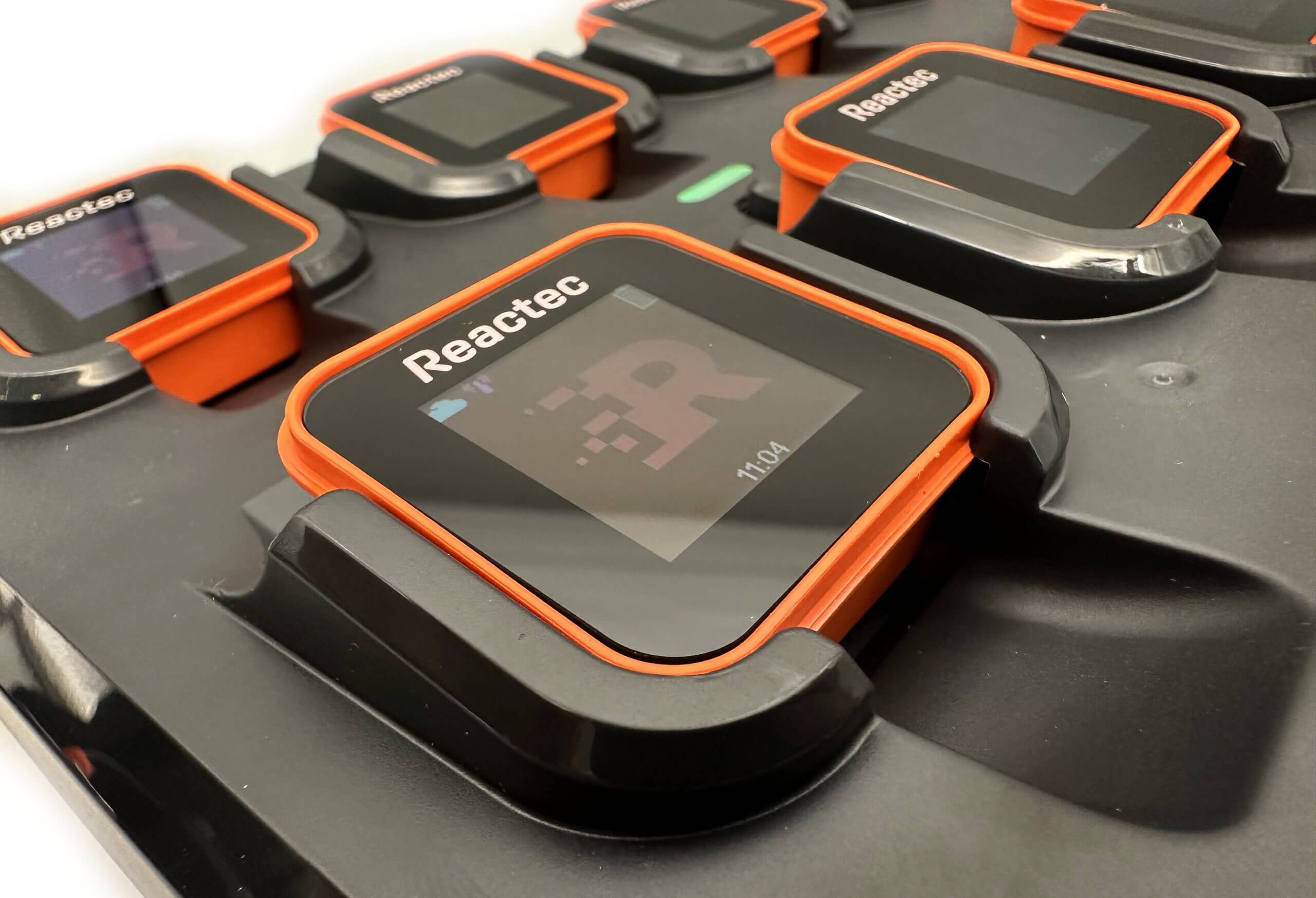
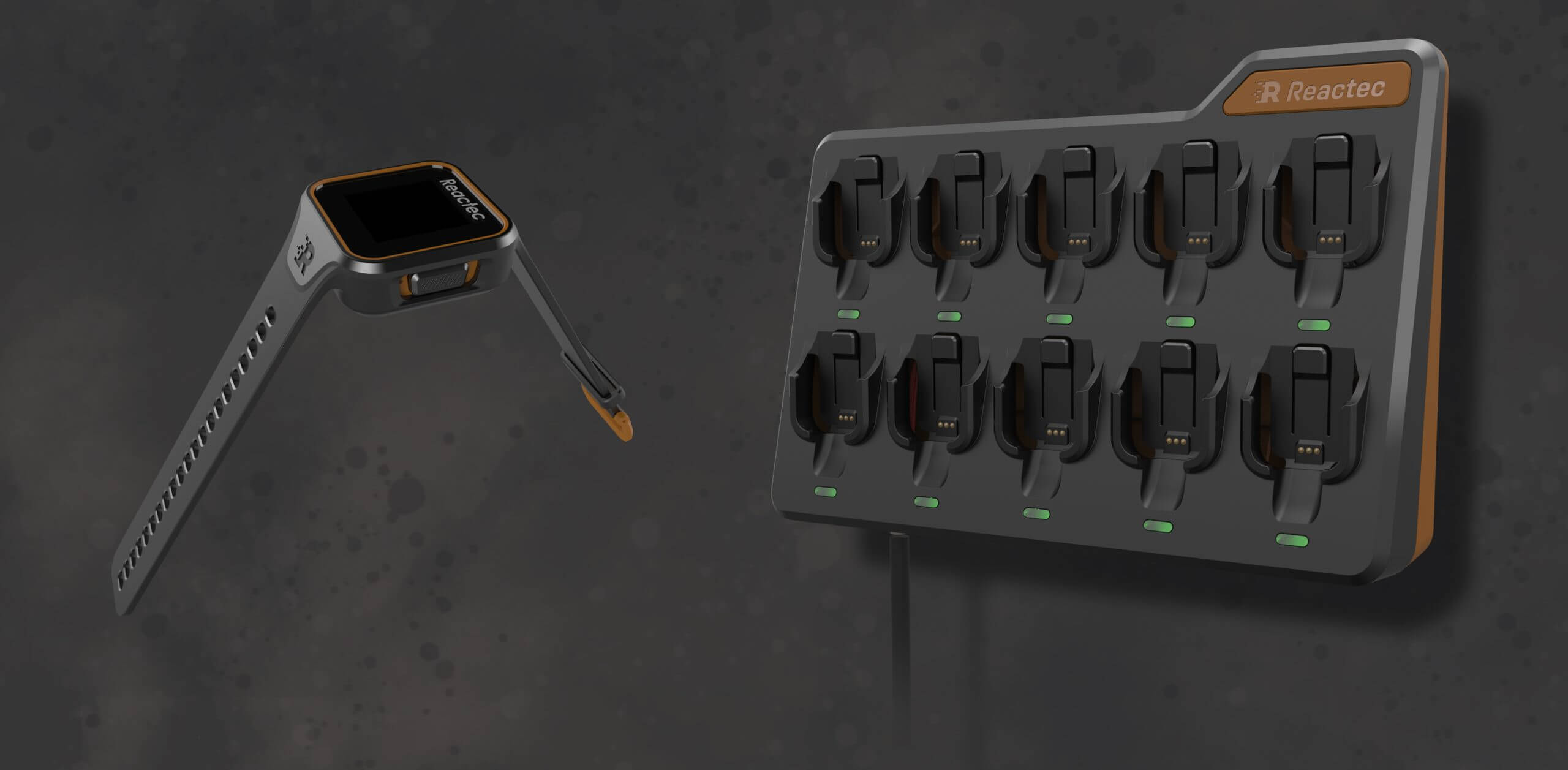
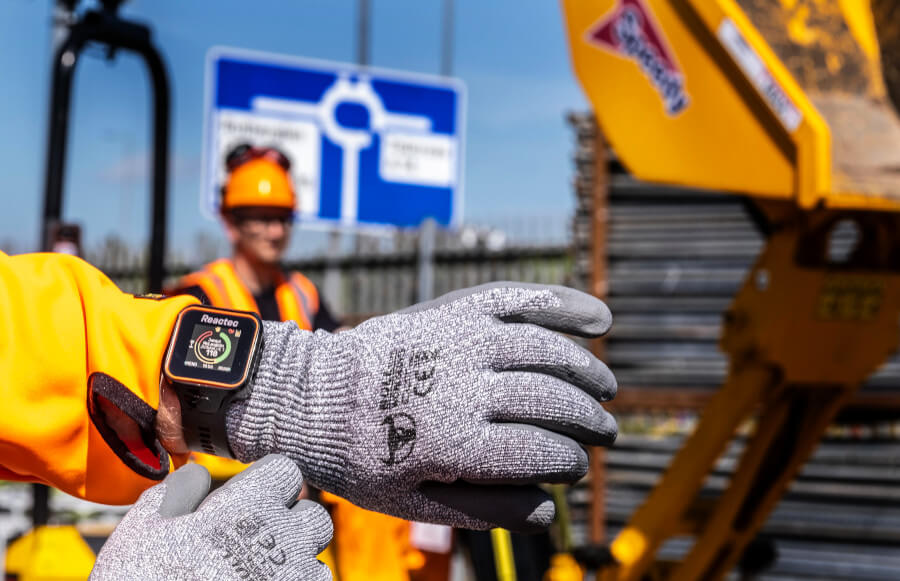
Explore Our Electronics Expertise
Discover how our multidisciplinary team can accelerate your next electronic device project. From concept to production, we deliver innovative solutions that combine our industry leading electronics and software design.
We like to find new, better and efficient ways of doing things. Contact us to discover how i4 Product Design can solve your current design challenge and take your product to the next level.
Schedule a call today
“i4 is an exceptional electronics design partner whose innovative solutions consistently exceed our expectations”